Investment casting, also known as lost-wax casting, is a manufacturing process to produce complex metal parts. It begins with creating a wax pattern, covering it with ceramic slurry containing refractory materials to form a ceramic shell mould, removing the wax and sintering the shell, pouring molten metal into the mould to form the casting part after solidification, removing the shell through vibration and water jet. Casting investment powder, containing refractory fillers like silica, zircon, aluminosilicates as well as binders, is a key material in the ceramic slurry formula and shell making process, playing an important role in surface finish, dimensional accuracy and integrity of the final casting parts. This article analyzes several key factors and conclusions regarding casting investment powder in the context of investment casting process.
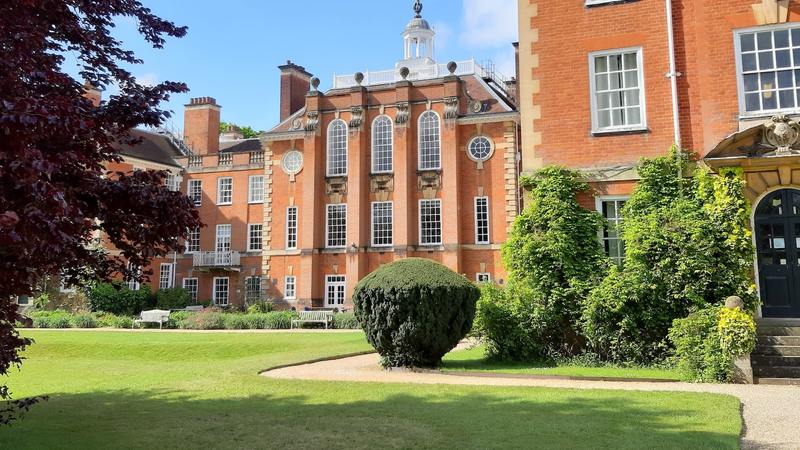
Casting Investment Powder Affects Shell Strength and Casting Surface Finish
The type and quality of casting investment powder directly impacts shell strength, hot tear resistance, as well as surface finish of final castings. Sub-standard powders with inferior refractory fillers may cause low shell strength, hot tearing issues like cracks and pores, as well as rough surface finishing. High purity powders containing premium refractory materials ensure high shell strength to withstand metallostatic pressure, improve tear resistance, and enable smooth casting surface resembling the wax pattern.
Particle Size Distribution Matters in Achieving Casting Dimensional Accuracy
Casting investment powder with proper particle size distribution is critical in achieving required dimensional accuracy per design tolerances. Well-graded powder containing a good mix of larger and finer particles significantly minimizes solidification shrinkage. On the contrary, powders with mainly fine particles tend to cause overpacking and larger linear shrinkage. Controlled powder grading also enables improved surface finish.
Quality Control Needed in Sourcing Reliable Casting Investment Powders
It is essential to implement stringent quality control when sourcing reliable casting investment powders from suppliers. Important parameters like refractory chemistry, LOI (loss on ignition), powder fineness, particle size distribution, loose bulk density must meet enterprise specifications. Suppliers certified with ISO 9001 quality management system generally offer more consistent powder quality. Periodic auditing of powder manufacturers is also necessary.
Casting Investment Powder Formula Tailored for Different Metal Alloys
There is no one-fits-all casting investment powder formula suitable for different alloys like steel, iron, aluminum, copper etc. Powder binder content and chemistry needs to be adjusted in accordance to the pouring temperature of the molten metal as well as chemical reactivity between shell and alloy elements. More research work is required to formulate tailored powder recipes that optimally balance key performance factors for each type of metal castings.
In investment casting process, the quality and properties of casting investment powder directly impacts multiple key performance indicators like shell strength, casting surface finish, dimensional accuracy, integrity of final castings. Proper control of powder factors enables high productivity and minimize defects.